All about chimneys: types, maintenance and choosing the right one
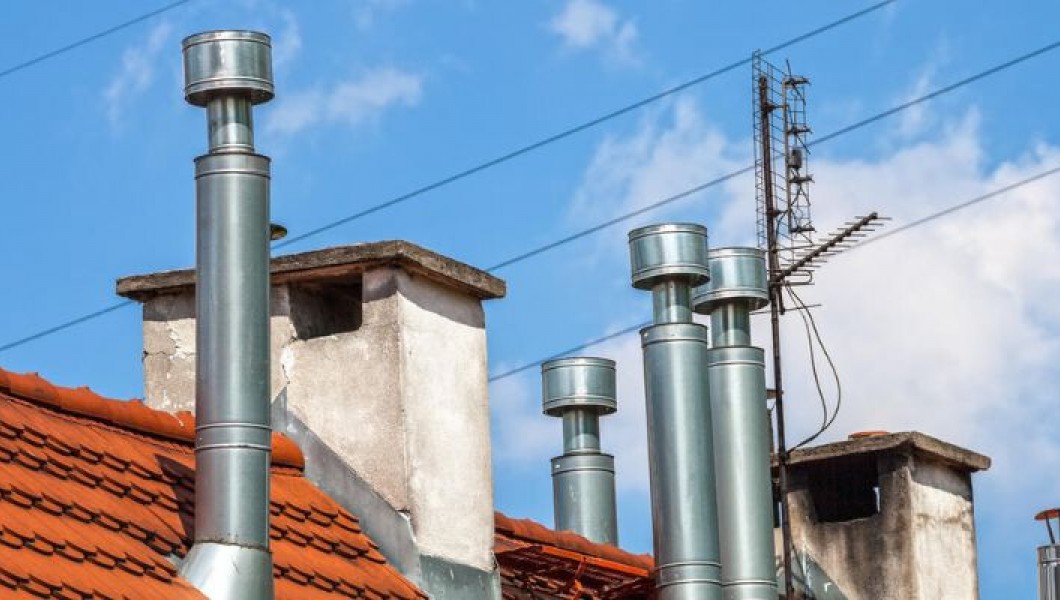
Origin and Evolution of Chimneys
Chimneys have played a key role in human history since ancient times. The first primitive forms of chimneys date back to when people began using fire for heating and cooking in their homes. In cave societies, smoke from fireplaces was simply vented through openings in the ceiling or through the entrance of the cave. Later, in ancient civilizations such as the Roman and Chinese, more organized structures for smoke ventilation began to be implemented, improving the quality of life and safety in homes.
During the Middle Ages, architectural advancements led to the emergence of stone chimneys, which were built as part of the walls of houses. This significantly reduced smoke in living spaces and allowed for more efficient heating. During this period, the first brick chimneys also became popular in Europe, used both in noble castles and in more modest homes.
With the advent of the Industrial Revolution in the 18th and 19th centuries, chimneys became an integral part of factories and large industrial complexes. During this period, metal chimneys also appeared, offering new possibilities for better durability and efficiency. Stainless steel (inox), which began to be actively used in the 20th century, provided a revolutionary solution for constructing chimneys that are more durable and easier to maintain.
Today, stainless steel and sheet metal chimneys are widely used in modern construction and heating systems. They offer flexible solutions suitable for different types of fuels and are preferred for their durability and efficiency. The development of these technologies has enabled the creation of lightweight yet strong structures that significantly improve energy efficiency and building safety.
Stainless Steel (Inox) Chimneys
Stainless steel (inox) chimneys are high-quality and durable solutions for venting flue gases. They are made of stainless steel, which has high resistance to corrosion, moisture, and acidic condensates. This makes them particularly suitable for heating appliances that use solid fuel, gas, or pellets.
Characteristics of Inox Material
Stainless steel (inox) is a special alloy that contains iron, chromium, nickel, and sometimes molybdenum. Chromium provides corrosion resistance by forming a protective oxide layer on the surface of the metal. Nickel further enhances strength and resistance to high temperatures, while molybdenum helps prevent acid corrosion.
Inox chimneys are most commonly made from AISI 304 or AISI 316 grade steel. The difference between them is that AISI 316 contains molybdenum, making it more resistant to aggressive chemicals and acids. This is important when fuels that emit acidic condensates are used.
Applications of Inox Chimneys
Due to their excellent properties, stainless steel chimneys are widely used in various fields:
- Residential heating systems – used for fireplaces, wood stoves, gas boilers, and pellet stoves and burners.
- Industrial facilities – suitable for factories and production plants where effective smoke venting is required.
- Restaurants and hotels – used in kitchens with professional ovens and grills, where efficient ventilation is essential.
- Boiler rooms – used for the safe removal of gases from large heating installations.
- Hospitals and laboratories – applied in systems for venting harmful fumes and gases.
Regulations and Requirements for Stainless Steel (Inox) Chimneys
To ensure the safety and efficiency of stainless steel chimneys, there are several European and national regulations that must be followed. The main standards include:
- EN 1856-1 and EN 1856-2 – define the requirements for metal flue systems, including temperature resistance, pressure durability, and acid resistance.
- EN 1443 – general characteristics of chimneys and their minimum safety requirements.
- ISO 9001 – quality management standard for the production of stainless steel chimneys.
- Local building regulations – depending on the country and region, there may be additional rules for the installation and operation of flue systems.
Advantages of Stainless Steel Chimneys
Stainless steel chimneys are a preferred choice due to several advantages:
- Durability – can last over 20 years without significant signs of wear.
- High-temperature resistance – withstand extreme heat loads without deformation.
- Corrosion resistance – protected against moisture and chemically aggressive gases.
- Lightweight construction – significantly lighter than brick and concrete chimneys, making installation easier.
- Smooth inner walls – reduce soot and condensate buildup, improving system efficiency.
- Modularity – easy to install and adapt to different heating appliances and architectural features.
Disadvantages of Stainless Steel Chimneys
Despite their many advantages, stainless steel chimneys also have some drawbacks:
- Higher cost – compared to sheet metal or brick chimneys, stainless steel chimneys require a larger investment.
- Precision installation required – for maximum efficiency, they must be professionally installed, which can increase costs.
- Additional insulation in low temperatures – for external chimneys, extra thermal insulation may be needed to prevent condensate formation.
Sheet Metal Chimneys
Sheet metal chimneys represent a more budget-friendly option for building flue systems. They are made of galvanized or stainless sheet metal, which generally has lower resistance to corrosion and high temperatures compared to stainless steel. Therefore, they are more suitable for temporary or less demanding heating installations.
Characteristics of Sheet Metal Chimneys
Sheet metal is a thin metal sheet produced from steel and can be processed using various methods to enhance its durability. The most commonly used types of sheet metal for chimneys include:
- Galvanized sheet metal – coated with a layer of zinc that protects the steel from corrosion. This type is the most widely used due to its affordability.
- Stainless sheet metal – contains chromium and nickel, providing higher corrosion resistance compared to galvanized sheet metal.
- Aluzinc sheet metal – a combination of aluminum and zinc that offers better resistance to high temperatures and external influences.
Applications of Sheet Metal Chimneys
Due to their low cost and ease of installation, sheet metal chimneys are widely used in various situations:
- Temporary heating systems – suitable for seasonal use or temporary construction facilities.
- Auxiliary buildings – such as garages, agricultural structures, and storage facilities.
- Backup or secondary chimneys – used as an alternative when the primary chimney is not functioning.
- Small industrial facilities – for example, workshops or small factories with limited budgets.
- Use in combination with insulation – in some cases, sheet metal chimneys are combined with thermal insulation materials to extend their lifespan and improve efficiency.
Regulations and Standards for Sheet Metal Chimneys
Although sheet metal chimneys are more affordable, they are still subject to regulations to ensure their safety and efficiency. The main regulatory documents include:
- EN 1856-1 and EN 1856-2 – define technical requirements for metal flue systems, including temperature and pressure resistance.
- EN 1443 – general characteristics and safety standards for all types of chimneys.
- Local building regulations – each country has its own specific rules for the installation and maintenance of sheet metal chimneys.
- Corrosion protection requirements – especially for galvanized models, which may rust over long-term use.
Advantages of Sheet Metal Chimneys
Sheet metal chimneys offer several key advantages, making them an attractive choice for specific applications:
- Low cost – one of the most affordable options for building a chimney system.
- Lightweight and easy installation – can be installed quickly without requiring complex tools or specialized equipment.
- Flexibility – can be easily shaped and adapted to specific structures.
- Suitable for short-term use – ideal for temporary heating solutions.
Disadvantages of Sheet Metal Chimneys
Despite their advantages, sheet metal chimneys also have some drawbacks:
- Susceptibility to corrosion – galvanized sheet metal can rust over time, especially in humid conditions.
- Shorter lifespan – compared to stainless steel chimneys, sheet metal ones have lower durability and wear out faster.
- Limited thermal resistance – not suitable for very high temperatures, especially if not protected with additional thermal insulation.
- Require regular maintenance – frequent cleaning and corrosion inspection are necessary to prevent damage.
Key Components of the Chimney System
The chimney system consists of several essential components that work together to ensure the safe and efficient venting of flue gases. Each element plays a specific role in the structure of the chimney and is crucial for its durability and functionality. Below is a detailed description of the main parts:
Flue Pipes
Flue pipes are the main part of the chimney and are the tubes through which the flue gases are vented from the heating appliance. They can be:
- Straight flue pipes – used for vertical sections of the chimney where no change in the direction of the gas flow is needed.
- Flexible flue pipes – used in complex installations where passing through narrow or curved spaces is necessary. They are particularly useful when renovating old chimney systems.
Flue pipes must be made of heat-resistant and corrosion-resistant materials, such as stainless steel or ceramics, to ensure durability and safety.
Brackets
Brackets are mounting elements that ensure the stability of the chimney system by securing the flue pipes and other components to the wall or ceiling. They are crucial for preventing shifts and vibrations that could compromise the system. Brackets are made of corrosion-resistant materials to withstand long-term operation.
Flue adaptors
Flue adaptors are used to connect different diameters and types of pipes within the chimney system. They are necessary when adapting the flue pipe to the specific requirements of the heating appliance or when making transitions between different materials (e.g., from a ceramic to a metal chimney).
Chimney Flashings
Flashings are used to protect the external part of the chimney from weather conditions such as rain, snow, wind, and UV radiation. They prevent moisture from penetrating the insulation and the chimney structure, which could lead to corrosion and cracking. Flashings are typically made of galvanized steel, aluzinc alloy, or stainless steel.
Rosettes
Rosettes are decorative and functional elements used where the chimney passes through walls, ceilings, or roofs. They also provide thermal protection by reducing the risk of overheating surrounding materials and preventing the accumulation of dirt around the chimney opening.
Tee Connectors
Tee connectors allow for branching of the chimney system, making it possible to connect more than one heating appliance to the same chimney. They are also used to create inspection openings for cleaning and maintenance. To ensure safety, when using tee connectors, the minimum distance between connected appliances and effective venting of flue gases must be maintained.
Elbows
Elbows are used to change the direction of the flue pipe. The most common types are:
- 45-degree elbows – used for smooth transitions when a slight change in direction is needed.
- 90-degree elbows – used in installations requiring a sharp turn, such as connecting a horizontal flue pipe to a vertical chimney.
Using too many elbows can reduce the chimney draft efficiency and hinder the proper venting of flue gases, so they should only be installed when necessary.
Heat Exchangers
Heat exchangers are additional devices installed in the chimney system to capture and utilize some of the heat contained in the flue gases. They work by redirecting part of the thermal energy back into the room or towards water heating systems, increasing the overall heating efficiency and reducing fuel costs.
Chimney Cowls
Chimney cowls are installed at the top of the chimney and serve several important functions:
- Prevent rainwater and snow from entering, which can damage the interior of the chimney.
- Reduce the risk of birds and insects entering the flue.
- Improve chimney draft by directing airflow and preventing backdraft.
There are various types of chimney caps, including static, rotating, and adjustable models, which optimize the performance of the chimney system depending on specific needs.
How to Choose the Right Chimney
Selecting the right chimney depends on several key factors, including the type of heating appliance, fuel, safety requirements, and the structural characteristics of the building. An improperly chosen chimney can lead to reduced heating efficiency, poor draft, and even risks of carbon monoxide buildup and fires. Here are some of the most important aspects to consider when choosing a chimney.
Type of Heating Appliance and Fuel
The type of heating appliance is the first factor to consider when choosing a chimney. Different appliances require specific chimney characteristics:
- Fireplaces and wood stoves – require chimneys with good thermal resistance and a large diameter for optimal draft. Insulated (double-wall) chimneys are often recommended for better efficiency.
- Gas boilers – use both single-wall and double-wall flue pipes but with a smaller diameter. Proper condensate drainage must be ensured.
- Pellet boilers and burners – require chimneys with good thermal insulation, as they operate at lower temperatures than wood stoves but generate condensate that must be effectively removed.
- Industrial and professional heating systems – often use large, insulated flue pipes resistant to acidic corrosion and high temperatures.
Difference Between Single-Wall and Double-Wall (Insulated) Chimneys
When choosing a chimney, it is essential to determine whether a single-wall or double-wall (insulated) flue pipe will be used. The difference between them is significant and depends on the specific application.
- Single-wall chimneys – made from a single layer of metal (stainless steel or sheet metal) and suitable for installation inside existing chimney channels or indoor spaces. They are more affordable but do not provide good thermal insulation, which may lead to condensation of flue gases.
- Double-wall (insulated) chimneys – consist of two layers of metal with an insulating material (mineral wool) in between. These chimneys are used for outdoor installation, where there is a risk of flue gas cooling. They reduce condensate formation, improve draft, and extend the service life of the chimney system.
Chimney Diameter and Height
Another critical factor when selecting a chimney is its diameter and height. If the diameter is too small, flue gases will not be vented efficiently, leading to backdraft and soot buildup. If it is too large, some of the heating appliance's efficiency may be lost.
The recommended chimney height depends on the type of heating appliance and the building configuration, but it is usually between 4 and 8 meters. Taller chimneys provide better draft, but they must be securely fastened, especially if installed externally.
Compliance with Regulations and Standards
When building a chimney, it is essential to comply with all applicable regulations and safety standards. Depending on local legislation, special insulation, corrosion protection, and fire-resistant materials may be required. The main standards applied to chimneys include:
- EN 1856-1 and EN 1856-2 – standards for metal flue pipes, defining their resistance to temperature, pressure, and corrosion.
- EN 1443 – general characteristics and safety requirements for chimney systems.
- Local building regulations – specify how chimneys should be designed and installed according to the region’s specific requirements.
Additional Considerations When Choosing a Chimney
In addition to technical specifications, several practical aspects should be considered:
- Installation complexity – some chimneys require more complex installation and professional setup, which may increase costs.
- Operating costs – double-wall chimneys typically require less maintenance and have a longer lifespan compared to single-wall options.
- Environmental impact – using durable and high-resistance materials reduces the need for frequent replacements and is a more eco-friendly solution.
Chimney Installation Instructions in 5 Steps
1. Building the Chimney Base
To ensure the chimney is stable and secure, it must be firmly attached to the ground or the building wall. There are three main installation methods:
- Wall mounting.
- Floor installation with a telescopic support.
- Floor installation on a concrete slab.
If you have chosen the third option, you can skip this step.
a) Installing a Wall Bracket
- Mark the drilling points.
- Drill holes and insert wall anchors.
- Secure the bracket to the wall with screws.
b) Securing the Telescopic Support
- Attach the telescopic support onto a flat concrete surface.
2. Installing the Inspection Element
The chimney stand serves as a base on which the inspection element is placed. This component is crucial for easy cleaning and maintenance.
At the bottom of the stand, there is a cap with a small opening and a drainage pipe that removes condensate, preventing moisture and soot buildup. It is essential to properly collect or divert the condensate rather than letting it drip onto the ground.
Installation:
- Attach the inspection element to the base of the stand, positioning the cap of the T-piece with the opening facing downward.
3. Installing the T-Piece and Wall Rosette
The T-piece is mounted above the inspection element and provides the connection between the chimney and the stove’s flue pipe using an adapter.
Steps:
- Place the T-piece on top of the inspection element.
- Slide the wall rosette onto the side pipe of the T-piece and connect it with the adapter.
4. Determining the Chimney Height
In this step, the flue pipes are stacked on top of each other until the desired height is reached.
Installation:
- Install the first flue pipe onto the T-piece.
- Secure it with a chimney bracket.
- Repeat the process until the chimney reaches the required height.
- Every 2 meters, fix the flue pipes to the wall using a bracket, positioning it at the connection point between two flue pipes.
Important:
If the roof eaves obstruct the vertical installation of the chimney, you can use:
- A flashing for sloped roofs
- A double elbow flue pipe to shift the chimney
5. Installing the Chimney Cap
The final step of the installation is placing the chimney cap. One of the advantages of this type of chimney is that it can be equipped with different types of caps, allowing for adaptation in case of a future fireplace change.
Installation:
- Place the finishing cap on top of the chimney.
Note:
The sockets of the flue pipes should always be oriented upward – in the direction of the smoke flow.
Connecting Multiple Heating Appliances to a Single Chimney
Connecting more than one fireplace or stove to the same chimney can be a convenient solution, but it requires careful planning and adherence to strict safety regulations. The primary requirement is that each heating appliance must have sufficient airflow to effectively vent the flue gases without creating backdraft.
Requirements and Recommendations:
- The chimney diameter must be large enough to accommodate the smoke from all connected appliances without causing gas retention.
- Use of tee connectors and special adapters to ensure proper gas flow direction and prevent the mixing of reverse airflow.
- Each appliance should be connected at a different level – when connecting multiple appliances, it is recommended to place the connections at different heights to avoid mixing flue gases.
- Avoid excessively long horizontal sections that can reduce draft and cause soot buildup.
- Install draft prevention dampers to ensure that smoke from one appliance does not enter another.
Potential Risks:
- Backdraft and smoke entering the room if the chimney lacks sufficient capacity or is improperly constructed.
- Carbon monoxide buildup, which poses a severe health risk.
- Reduced efficiency of heating appliances if the chimney cannot provide adequate draft.
- Fire hazard if the installation is not done correctly and fire safety measures are not followed.
If you plan to connect more than one fireplace or stove to a single chimney, it is best to consult a professional chimney sweep or heating system specialist. This will ensure that the construction is safe and efficient.
Chimney Maintenance and Cleaning
Proper maintenance and cleaning of chimneys, whether stainless steel or sheet metal, are essential for the safety and efficiency of the heating system. Regular cleaning prevents the buildup of soot and condensate, which can lead to blockages, reduced draft, and even a fire hazard.
Cleaning Stainless Steel (Inox) Chimneys
Stainless steel chimneys are resistant to soot buildup due to their smooth inner walls, which make it difficult for residue to adhere. However, when using solid fuels such as wood or coal, regular cleaning is necessary. It is recommended to inspect and clean the chimney at least twice a year. Cleaning methods include:
- Mechanical cleaning – using brushes with metal or plastic bristles.
- Chemical treatments – using powders and granules that dissolve soot and prevent buildup.
- Professional services – hiring specialists with professional equipment for thorough cleaning.
Cleaning Sheet Metal Chimneys
Sheet metal chimneys are more susceptible to corrosion, especially if exposed to moisture or if the fuel produces acidic condensates. Therefore, their maintenance requires even more careful attention. Key recommendations for cleaning sheet metal chimneys include:
- Mechanical cleaning at least twice a year – using appropriate brushes to prevent soot buildup and rust formation.
- Anti-corrosion protection – applying special protective coatings to extend the chimney’s lifespan.
- Inspection for rust and damage – regularly checking the sheet metal chimney for signs of wear and taking timely action.
- Use of chimney caps – preventing rain and moisture from entering, which accelerates corrosion.
The general rule for all types of chimneys is that maintenance should be performed regularly and in accordance with the manufacturer’s recommendations. This ensures their safety, efficiency, and durability.
10 Most Common Chimney Problems and Their Solutions
Chimneys can encounter various issues during their operation, leading to reduced efficiency, air pollution, or even fires. In this section, we will discuss the 10 most common problems and how they can be resolved:
Poor Chimney Draft
Problem: The chimney fails to efficiently draw out smoke, causing the room to fill with smoke.
Solution: Check the height and diameter of the chimney—incorrect dimensions can cause poor draft. Installing a chimney cap can improve airflow.
Backdraft
Problem: Smoke returns into the room instead of rising upwards.
Solution: This may be caused by a clogged chimney, lack of sufficient incoming air, or improper construction. Ensure the chimney is clean and that the room is well-ventilated.
Blockage from Bird Nests or Insects
Problem: Birds often nest in chimneys, while spiderwebs and insects can create obstructions.
Solution: Install a chimney screen or a special cap to prevent animals from entering.
Condensation and Moisture Buildup
Problem: Water vapor condenses inside the chimney, leading to corrosion and wall deterioration.
Solution: Using double-walled insulated chimneys and ensuring proper ventilation can help reduce condensation buildup.
Corrosion of Metal Components
Problem: High humidity and acidic compounds in smoke can cause rust and damage.
Solution: Use stainless steel for better durability and regularly inspect the chimney for signs of corrosion.
Soot and Creosote Buildup
Problem: Soot and creosote can accumulate on chimney walls, increasing the risk of fire.
Solution: Clean the chimney regularly, especially if using solid fuels like wood or coal. Using dry wood and chemical cleaning agents can help reduce buildup.
Cracks and Structural Damage
Problem: Over time, brick and metal chimneys can crack or deteriorate.
Solution: Small cracks can be repaired with heat-resistant materials. Severe damage may require partial or complete chimney restoration.
Air Currents Affecting Draft
Problem: Wind around the chimney can interfere with proper smoke expulsion.
Solution: Install a draft-deflecting cap to improve draft and minimize the impact of external conditions.
Overheating and Chimney Deformation
Problem: Excessively high temperatures can cause expansion and damage to chimney components.
Solution: Using heat-resistant materials and double-walled chimneys can reduce the risk of overheating.
Compatibility Issues Between the Heating Appliance and Chimney
Problem: If the chimney is not properly designed for the type of fuel or heating appliance, it can lead to inefficient combustion and poor draft.
Solution: Consult a specialist before purchasing a chimney to ensure it is suitable for your heating system.